Substation & Switchyard Design Considerations: Size, Load, Cost
Engineers must weigh costs against performance and reliability to create systems that are both effective and affordable.
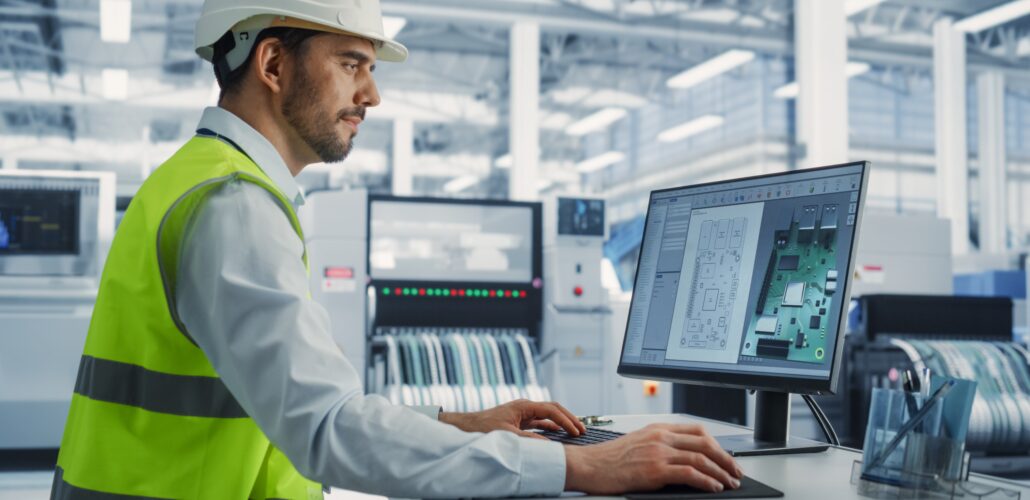
Image for illustration purposes.
Switchyards and substations are vital for moving electricity from power plants to your house. They’re packed with gear like disconnectors, circuit breakers, and transformers, all working together to dispatch power. When designing these facilities, engineers must carefully juggle size, load, and cost. It is essential to possess a solid understanding of switchyard switching schemes and substation equipment like transformers, circuit breakers, disconnectors, and busbars for safe operation when locating and identifying faults.
Switching it Up:
Different ‘switching arrangements‘ exist, which are how everything’s connected. The goal? To keep the power flowing even when bits need fixing. This involves designing with busbars. Busbars are large conductors that act like electrical highways, connecting generators, transmission lines, and feeders.
Single busbar systems are cheap and simple, but a fault shuts everything down. Double busbar systems offer more flexibility, allowing parts to be isolated for maintenance without a full outage. One-and-a-half breaker schemes use three circuit breakers for every two circuits, boosting reliability further but at a higher cost. A bus sectionalizer divides the busbars into sections so they can be easily isolated from each other.
Sizing:
Because of the kit used and the voltages involved, most of this gear is outside. Substations, by contrast, can be indoors and are near where the power is needed. Big gear like transformers and oil circuit breakers sit on concrete bases. Lighter bits are mounted on steel frames, making it easier to make changes. These structures are classified into unit, truss, and ground – the equipment is mounted on the concrete structure, and the lighter equipment is mounted on steel frames, making additions, modifications, and changes easy to make.
Earthing is Key:
Proper earthing (grounding) is a must for safety, to protect both people and the kit. All metal bits that don’t carry current – fences, cable trays, metal structures – must be connected to earth. This provides a low-resistance path for fault currents. This means that when a fault occurs, the conductor size matters because it provides a low resistance path to the conducting part of the earth. Often, grounding rods and metal plates are used.
Grounding rods can include galvanized pipes, stainless steel, copper clad, or solid copper rods. When the rod or plates can be installed below the permanent moisture level or if the ground is loose, dry, or sandy, its resistance is apt to be high, and the soil should be treated. Often, engineers dig a trench about 18 inches deep and fill it with rock salt, copper sulfate, or magnesium sulfate.
Maintenance:
Although rugged and weatherproof, switchyard kit still needs looking after. Batteries, oil circuit breakers, and transformers all need regular testing and inspection. Areas exposed to pollution from smoke or dust need regular cleaning to prevent flashovers. Aside from the maintenance schedule, the operator should observe the equipment for unusual conditions whenever they enter a switchyard or substation.
Source: EEPower
#busbar arrangements#circuit breakers#disconnectors#earthing systems#Electrical safety#fault currents#grid reliability#grounding rods#high-voltage equipment#maintenance#plot plan#power distribution#Power Grid Stability#power system components#protection schemes#single-line diagram#substation design#switchyard layout#transformers#unit substations